Long before Dr. Ralf Dupont founded Levicron, it was clear to him that this business could not be built up based on suppliers and sub-contracted work because of the required part precision. Thus, a vertical business integration, including bespoke machining and process development, shaft and bearing parts, was part of his business plan right from the beginning.
Therefore not only 97% of the parts and components of their products are developed, manufactured, and tested in-house. The entire service work, customer support, and process development with and for our products to support our customers before and after purchasing comes from Levicron.
Hence our Slogan: Ultra-Precision meets industrial Grade
Calculating and simulating bearing characteristics and shaft dynamics is only half the way you need to go to reach your destination. But to use analytics, FE Analysis, and CFD Analysis to optimize the later product performance is way more important to provide your customer with the optimal spindle solution for his application. Thus in Levicron, bespoke analytical methods and FE simulation tools are combined in closed loop optimization cycles based on genetic and population-based algorithms. The shaft, bearing and jet geometries as input variables deliver their optimal sizes after a multi-objective optimization cycle. The multi-dimensional objective and solution space can be defined for any application, whether it is robustness, optimal dynamics, or the best compromise. This process is affected by issues like they are known as natural genetic coding, information degeneration, tail degeneration, or elitism.
For spindle products from Levicron the following analytical and numerical development tools are used:
- Analytical methods for the performance description of non-contact bearing systems
- FE Structural Analysis for the prediction of centrifugal load or temperature caused deformation
- Numerical Fluid Dynamics to predict the flow characteristics and the local thermal conductivity of bearing gaps and cooling jackets
- Open loop optimization (1-way FSI) of Analytical, CFD, and FE Analysis to predict deformations and their influence on bearing performance and shaft dynamics
- Closed loop evolutionary, analytical optimization for bearing and shaft geometries based on weighted functions to get optimal bearing performance and shaft dynamics
- 3D CAD/CAM for production parts modeling
- CAD/CAM for production drafting
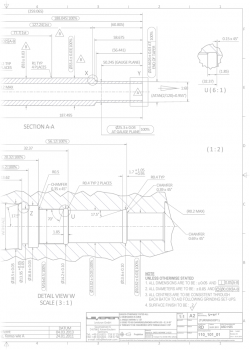
Manufacturing one of our spindle shafts requires more than 20 single manufacturing steps where every step must be matched to the previous one. Finish drawing is not helpful here.
After creating a 3D model of each part of a spindle assembly and the final spindle assembly model, production models are derived. These include dimensions and allowance for the next machining step. These production models now allow the derivation of station drawings that define dimensions, shape, and position tolerances and the allowance for each machining step.
Even before setting up a business plan for Levicron, it was clear that manufacturing ultra-precision spindles production technology and internal manufacturing would be a very part of the success. Dr. Ralf Dupont knew that no sub-contractor could be used for the required part precision with his sound knowledge of manufacturing techniques – Grinding, Diamond-Turning, and Laser-Drilling in particular. The result of trying sub-contractors for standard turning and milling work at the beginning confirmed his thoughts. Part quality and the suppliers’ reliability didn’t comply with what was needed.
As a result, Levicron vertically integrates 90% of the production technologies required to manufacture ultra-precision motor spindles. It can now offer bespoke solutions to its customers and rapid customer support and turn-around time. Production Technologies developed and used in Levicron include:
- CNC Turning (with and without life tooling)
- CNC Milling (3 and 4 Axis Machining)
- CNC Cylindrical Grinding
- CNC Bore Grinding
- CNC Diamond Turning
- Flat Grinding
It includes bespoke machining solutions which contribute to the precision and quality of Levicron Spindle Products.
An error or mistake during the manufacturing process often can be seen during testing, but the way of the affected part (s) in between can be long and can cause financial losses and a tremendous loss in time. Thus all parts and assemblies are measured and tested by the corresponding station drawing.
While dimensions and diameters often can reliably be checked with gauges or micrometers, shape – like cylindricity – and orientation – like squareness – require CNC form measurement. CMMs and Form Testers are part of our inspection to ensure part quality.
Measurements of each part are recorded and stored in protocols to keep track of single features in different batches. For this, production and inspection control is essential and is done with our MRP system.
The modular design of our spindle products allows us to assemble, test, and store sub-assemblies, which can then be used to create and test the final product in a short time. Thus we store bearing cartridges, spindle bodies, and flange units to be ready for your order at any time.
To get to this point, much development and optimization work were necessary. As a result, turnover and lead time are much shorter than any other spindle manufacturer.
Before a spindle is built from the modules, all sub-assemblies are tested by different performance and accuracy tests. For example bearing system, tool clamping, spindle encoder, and motor are tested before a bearing cartridge goes to stores. For the final testing, our spindle products get tested with different static and dynamic short and long-term tests. These include:
- Tool change cycling and final tool clamp approval
- Static radial and axial load capacity tests
- Determination of the axial and radial concentric static spindle stiffness
- Multi-step coolant jacket leak-down tests
- Dynamic testing with drive data recording
- Motor stress tests
- Dynamic run-out and vibration recording with speed
- Spindle Error-Motion verification
- Long-term spindle run with final approval
For the dynamic behavior and ultra-precision at high speed, dynamic balancing is crucial to get the qualities of the spindle we promise our customers. Our tool spindles leave our premises with a balanced quality of better G0.05 mm/s at 60.000 rpm measured in three planes. It’s obvious that no commercially available dynamic balancing to such values can be used. Thus Levicron developed unique and bespoke balancing rigs for their spindle and tool holder products.
It also applied to our HSK tool holder series UTS-x. While the industry standard specifies G2.5 mm/s at 25.000 rpm Levicron sells their tool holders with G0.3 at 60.000 rpm and are thus 20 times better concerning balancing than the industry standard DIN69893. The residual imbalance and the tool clamp repeatability can be measured and verified by our 4×90° reversal test. For our tool spindles AS-H25 and ASD-H25A, we specify a tool clamp repeatability of better 0.2 microns if used with our HSK tool holders UTS-x that comply with DIN69893.
Our aerostatic spindle solutions comply with the current standard for CNC tool spindles. It includes the spindle encoder, the liquid cooling, the synchronous motor, and the tool change. However, the end customer and the machine builder can save much time by using our sound knowledge of setting up, optimizing, and running our spindles.
Our Spindle Retro-Fit and Integration Kits offer this service for any common machine control and spindle drive. Get more information on our Retro-Fit and Integration Kit page.
The same applies to a service case. Together with a motivated team of skilled engineers, we support you quicker than expected.